Art Becomes Science
- mbharch
- Jan 5, 2023
- 5 min read
Updated: Jan 29
LD+A Magazine | January 2023 by Michele Zimmerman
A landmark building on the campus of UC Berkeley undergoes an overhaul that suits its new role while honoring its past.
Once an art museum and film archive, and now a life-science facility, the Bakar BioEnginuity Hub rests inside a historically significant Brutalist structure with a modern makeover on the campus of the University of California, Berkeley. After the building was deemed seismically unsafe and the Berkeley Art Museum vacated in 2014, MBH Architects stepped up in 2016 to rework the architecture and lighting design of the nearly all concrete, irregularly shaped build-ing. MBH’s mission was to pay homage to Mario Ciampi’s original design from 1970 while creating a coworking space that would bridge gaps between graduate students, life-science start-ups and established biotech groups.

The building opened in 2022 after extensive renovations including a 6,600-sq ft glass-fronted laboratory addition, auditorium, collaboration spaces, conference rooms, two public plazas sharing a landscaped walkway, private offices and an undergraduate workspace. Pre-existing skylights were replaced, upper-level galleries were trans-formed into laboratories and pre-existing cantilevered ramps were repurposed. To execute the design, MBH had to overcome unorthodox angles, varying ceiling heights, lighting requirements for different types of workspaces, and, finally, strict energy restrictions.

To combat drastic architectural differences while making as few changes as possible to the structure itself, designers took to 3D visualization as well as help from electrical engineers and light-ing representatives to ensure smooth transitions between spaces. “We were able to evaluate light fixtures over time, until we found fixtures that both technically worked and spoke the same aesthetic language as the existing historical building. We were inspired by the original lighting design and implemented round lighting fixtures that smoothed the contrast between the geometric ceilings and a synchronized lighting layout,” says Studio Director Ken Lidicker.
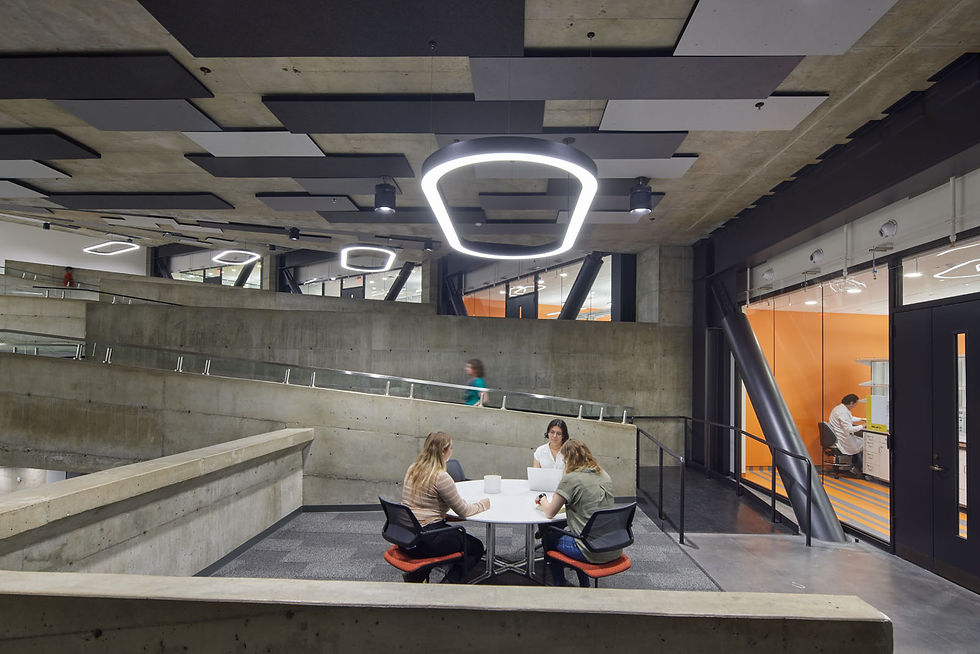
These round and oval luminaires are thematically incorporated throughout the space. For example, thin-profile, oversized, circular fixtures in the main lobby (Zumtobel) directly call back to the luminaires that were previously recessed into the area’s short ceilings; large elliptical pendants (Finelite) announce each new tier in the upper-gallery labs and help to orient visitors; and oval pendants were custom made, in collaboration with MBH, Finelite and Associated Lighting Representatives, for further wayfinding on cantilevered ramps.
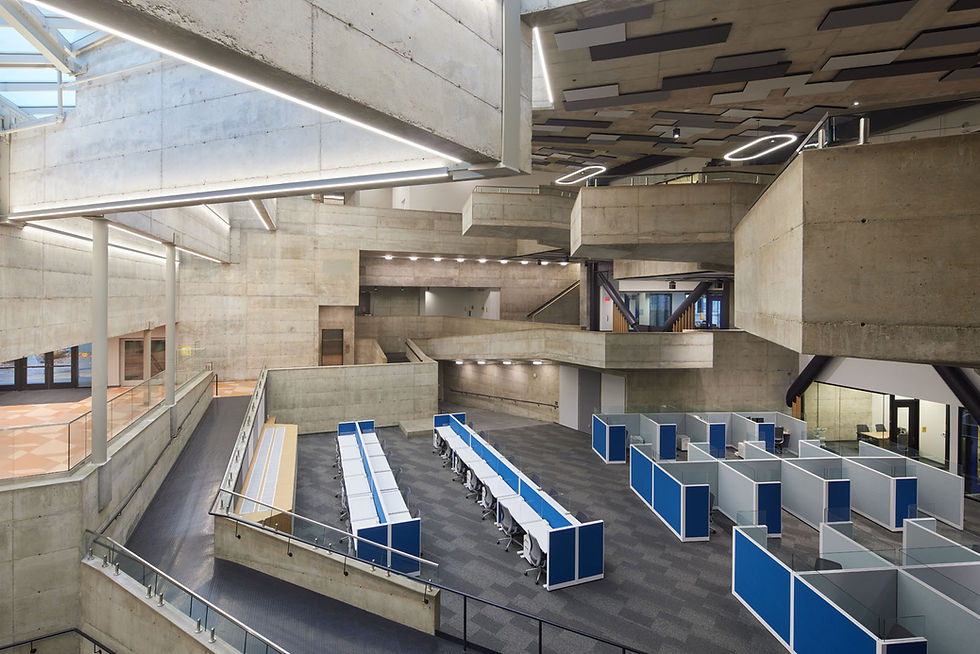
The ramps “serve as the focal point and journey to each level,” says Lidicker. In addition to the oval pendants which provide ambient light, designers used “integrated LED wall bases to make [the ramps] more inviting. Because of the angles of these ramps and the concrete floors, walls and ceiling surrounding them, detailing the ramps was tricky. Baseboard lighting allowed us to achieve the desired footcandles on the walking surfaces without breaking the amazing view of the cantilevered ramps.” Designers aimed for a 20-fc target on the ramps.
The 3,100 sq ft of skylight above the lower gallery also merges form and function. When the building was used to house light-sensitive artifacts, the skylights were darkened. But in its new life as the Bakar BioEnginuity Hub, designers uncovered and “replaced weather-opaqued skylights with new translucent glass,” says Architectural Job Captain Marlene Hurtado, MBH. This change allows for natural daylight and enhances the visitor experience. Artificial linear lights (Focal Point) were placed inside skylight pockets to enhance the interior illumination even further. Custom lengths of Seem 1 Direct/Indirect fixtures range from 4-ft to 10-in. long and 45-ft to 9-in. long. “Of all the key lighting moments in the building, the lights around the skylight are the most impactful in terms of cre-ating a well-lit interior space and making a striking visual,” says Lidicker. “The high-output up/down light source helped us achieve the desired task lighting levels (50-fc average) needed at the open offices under the skylights. These lights exceeded our expectations by accenting the concrete beams and skylight while also being visible from the exterior of the building, since the light is directed up along the concrete walls. If [visitors] stand at the top of the interior ramps at night, these skylight lights bring the double-height space to life.”
One key accommodation involved task lighting at the various workstations. Hurtado says, “Due to the vast difference in ceiling conditions throughout the building, not all task lighting could be uniformly designed. For instance, some work-stations are in ‘normal’ ceiling spaces of 8-ft tall white acoustic ceiling tiles, while next to them are workstations with 40-ft high concrete ceilings.” For example, in upper-gallery ceilings designers implemented high-output theater lights between acoustic felt panels. “These light fixtures are all black with a minimalist form, making them a perfect source that blends into its surroundings and provides the right amount of illumination,” says Hurtado. In lab spaces designers implemented suspended up/downlights for a soft ambient glow above tall-workstation benches and direct task light on work surfaces. AFX lights are magnetically mounted to the undersides of lab-casework shelving to provide user-controlled task lights with the option of three different color temperatures.
While the overall strategy for interior color temperature was warm light set to 3000K and 3500K, the strategy for the exterior was to play up the boldness of the building’s character with lights set to a cooler 4000K. The team implemented a myri-ad of exterior fixtures in the public zones to create an inviting place to rest along the two nearby streets. Fixtures included in-ground lights (ERCO); LED handrails; light poles and low bollards (Tech Lighting); overhang lights; under-tread lights (Kelvix Lighting) and wall washers (Hydrel). In illuminating the exterior, designers faced unexpected challenges due to pandemic-related supply-chain delays. MBH performed a collective balancing act: waiting for the perfect lighting fixtures to arrive versus making the tough decision to substitute different fixtures for those they had intended to use.
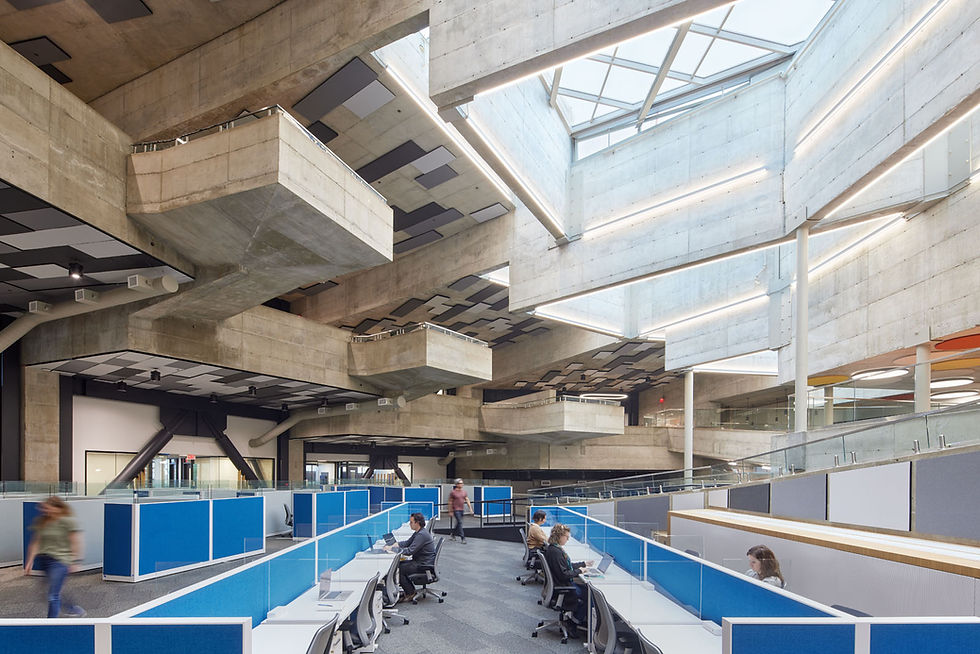
To align with the university’s energy goals and meet the standards for LEED Gold Certification, much of the building needed to be brought up to code. Acoustic and seismic performance, as well as water intrusion, were addressed along with a complete overhaul of light fixtures and electrification. To preserve as much of the historical space as possible, designers repurposed existing pathways and lighting locations. “We upgraded all lighting to LED fixtures with stringent lighting control schedules in order to maximize daylight from the skylight and improve the experience within the building,” says Lidicker. The zero-carbon operational, all-electric system made a huge difference in energy efficiency for the massive project. Now that the BioEnginuity Hub is operational, Hurtado says, “the building performs 20% better than California Energy Code (Title 24) requires and has an Energy Usage Intensity (EUI) of 81 kBtu per sf ft year, a 33% reduction when compared to the LEED baseline and a 63% reduction when com-pared to similar labs in the Labs21 database.”
THE DESIGNERS
Marlene Hurtado is an associate and architectural job captain with a focus in interior and lighting design at MBH Architects.
Ken Lidicker is a senior asssociate and studio director at MBH Architects.
Kevin Koblik was formerly a senior associate and project manager at MBH Architects.
By Michele Zimmerman
Published: LD+A Magazine